The Importance of Male Connectors in Industrial Applications
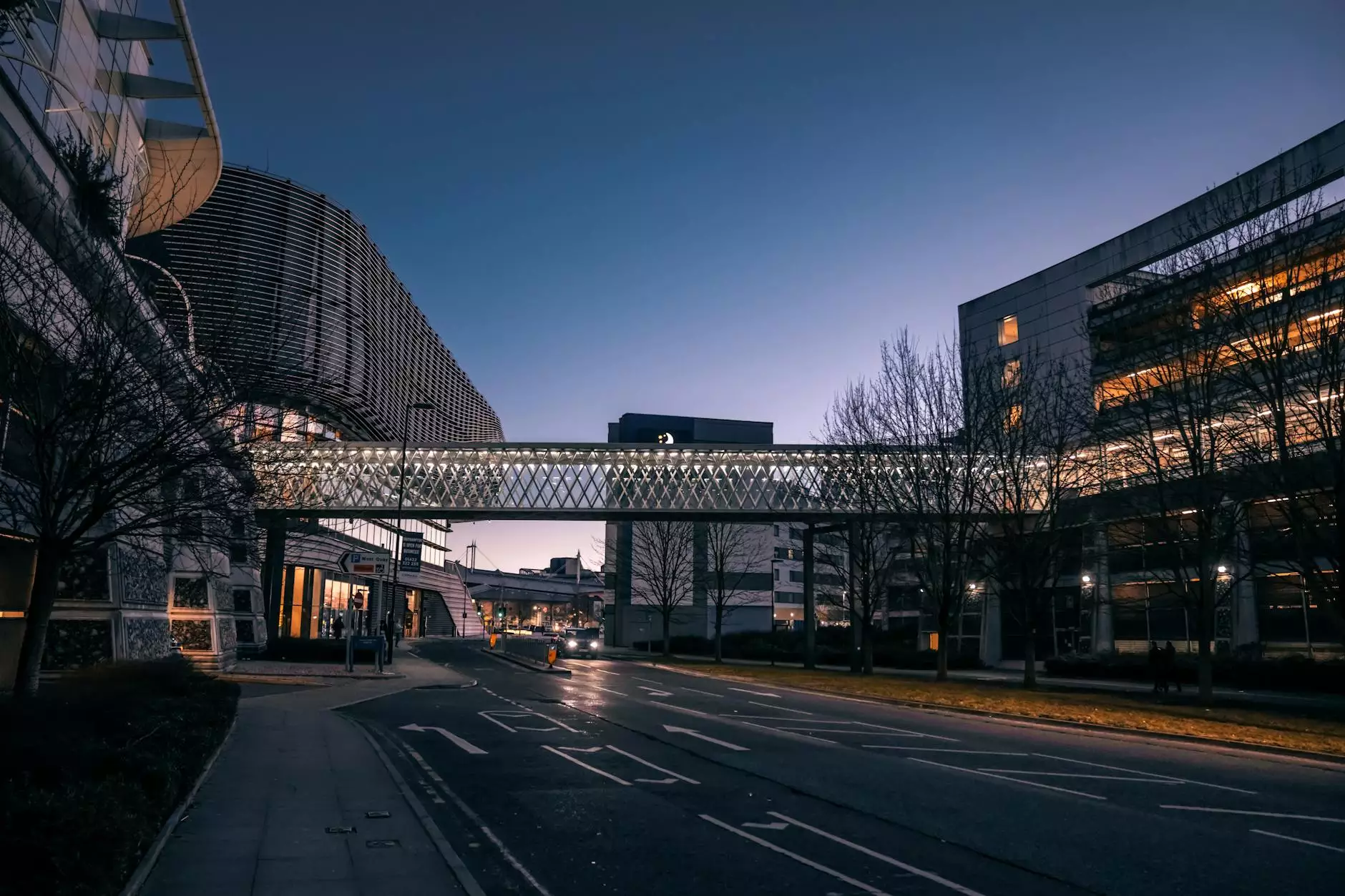
Male connectors are essential components in various industries, facilitating efficient and reliable connections in fluid and gas systems. As a part of a broader range of hardware, including tube fittings, ferrule fittings, and valves, understanding the role of male connectors can optimize operations and enhance system performance.
What Are Male Connectors?
In technical terms, a male connector refers to the protruding end of a connector system designed to fit into a corresponding female connector. This design mechanism allows for a secure, airtight connection that prevents leaks and ensures the integrity of the system in which they are employed.
Applications of Male Connectors
Male connectors find their use in a variety of applications across multiple sectors. Below are some notable uses:
- Fluid and Gas Transport: Male connectors are crucial in connecting pipes and tubes in systems that transport fluids or gases.
- Instrumentation: Used in various instruments that require a secure connection to measure or control process variables.
- Manufacturing: Incorporated in assembly lines to connect hoses and pipes in pneumatic and hydraulic systems.
- Automotive: Essential in fuel and fluid lines for reliable connections that are resistant to environmental factors.
Types of Male Connectors
There are numerous types of male connectors available, each tailored for specific applications. Here's a detailed look at some popular varieties:
1. Tube Fittings
Male connectors in the form of tube fittings are widely used to connect tubes for fluid transport. These fittings ensure a leak-free connection, enhancing system reliability.
2. Ferrule Fittings
In ferrule fittings, male connectors play a role in sealing connections through the use of ferrules that compress the tubing in place. This results in a secure connection that can withstand high pressure.
3. Threaded Pipe Fittings
Threaded male connectors provide robust connections for piping systems. These connectors are easy to install and maintain, making them a popular choice in various industries.
4. Flanges
Flanged male connectors allow for easy connection and disconnection of pipes. They are widely used in industrial systems where maintenance is frequent.
5. Valve Connectors
Check Valves
Male connectors in check valves ensure smooth flow in one direction while preventing backflow, vital in preventing system failures.
Ball Valves
These connectors are essential in ball valves, where they enable quick access to control fluid flow, vital in various industrial processes.
Needle Valves
Male connectors in needle valves provide precise control over flow rates, making them crucial in applications requiring accuracy.
Manifold Valves
Used in manifold systems, male connectors are key to centralizing control for multiple circuits, hence optimizing operational efficiency.
Advantages of Male Connectors
The use of male connectors in industrial applications offers numerous benefits, including:
- Reliability: Male connectors provide sturdy and stable connections that are less likely to leak compared to other connection methods.
- Versatility: They can be utilized in various applications, making them indispensable in many industries including both manufacturing and service sectors.
- Ease of Installation: Many male connectors come with intuitive designs that lead to straightforward installation procedures, reducing downtime during maintenance.
- Durability: With materials designed to withstand harsh industrial environments, male connectors have long service lives, minimizing replacement costs.
Choosing the Right Male Connector
When selecting the appropriate male connector for your application, consider the following factors:
- Material: Choose materials compatible with your process media; for instance, stainless steel is ideal for corrosive environments.
- Size and Thread Type: Ensure the connector fits your existing piping systems based on size specifications and threading standards.
- Pressure Ratings: Assess the pressure requirements of your system to choose a male connector that can handle operational loads.
- Application Requirements: Factor in whether your application necessitates flexibility, rigidity, high flow, or pressure control.
Maintenance and Care of Male Connectors
To ensure the longevity and functionality of male connectors, regular maintenance is important. Here are some essential maintenance tips:
- Regular Inspections: Inspect connectors for signs of wear or damage, particularly in high-stress or high-pressure environments.
- Cleaning: Keep threads and sealing surfaces clean from debris to ensure tight, leak-free connections.
- Lubrication: Applying appropriate lubricants can enhance connection longevity, especially in threaded and rotating systems.
- Replacement: Replace any connectors showing significant wear or damage before they lead to leaks or system failures.
Conclusion
In summary, male connectors are a vital component in the assembly of industrial systems involving pipe and tube fittings. Their ability to provide secure, durable, and reliable connections makes them indispensable in applications ranging from fluid transport to precise control in valve systems. By understanding the different types, applications, and advantages of male connectors, businesses can make informed choices that enhance performance and efficiency.
For those looking for high-quality male connectors and related products, explore the selections available at Tech Tubes. With a variety of tube fittings, ferrule fittings, forged pipe fittings, and more, you are sure to find the ideal components for your needs.